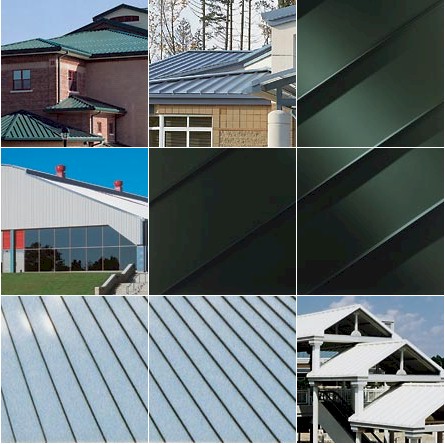
Original
Grandrib 3® and Grandrib 3® PLUS profiles, with
their clean traditional lines, are manufactured from
only the best prime quality structural steel
available—no seconds ever! Our drive to be the
best means that we start with the finest materials
and finish it with a premium coating system—Super
Alurite® 2000.
Whether your application is new or old, commercial,
agricultural or residential, Fabral's panels and
paint systems are designed to exceed your
requirements and expectations. Make Grandrib 3® or
Grandrib 3® PLUS panels your choice for all your
metal panel building needs.

Specifications
- The original
time-tested profile
- 29 ga. structural
quality, full-hard steel
- 10 layers of
protective coating
- High-performance
Super Alurite® 2000 paint system
- Class 4 hail
impact resistance (UL 2218)
- Class A fire
resistance rating (UL 790)
- Anti-siphon
sidelap design for excellent weathertightness
- Custom cut to
lengths up to 40'
Color
Charts
Colors
shown will vary based on your monitor type and
settings. Actual metal samples are available. Due to
product improvements, changes and other factors,
FABRAL reserves the right to change or delete
information herein without prior notice.
Metal
Roofing Warranty
- Grandrib 3®
Warranty
- Standard
galvanized coating
- 30-year
non-prorated film integrity warranty for
walls and roofs
- 25-year
warranty against fade and chalk for walls
and roofs
- Grandrib 3®
Plus Warranty
- Heavy duty
galvanizing for long-term corrosion
resistance
- 35-year
non-prorated film integrity warranty for
walls; 30 years for roofs
- 25-year
warranty against fade and chalk for walls
and roofs
- 10-year edge
rust warranty against acid rain
- 25-year
non-perforation warranty against acid rain
for walls, 20 years for roofs
Metal
Roofing Installation
Use
the links below to download installation
instructions found on this page in PDF or Microsoft
Word format:
Building
Design and Construction
To ensure adequate
performance and longevity, protect metal panels from
potentially corrosive situations and materials. When
treated lumber will be in direct contact with metal
panels please note the following: Galvanized steel
is compatible with the CCA (Chromated Copper
Arsenate) pressure-treated lumber that is
predominantly used today, but not with the older
Penta treated lumber. Aluminum, however, must be
separated from contact with all treated wood since
the chemical preservatives are corrosive to
aluminum. Likewise, dissimilar metals also require a
protective barrier between them to prevent galvanic
corrosion. Request FABRAL Technical Bulletins #803,
106, and 107 for more information on treated lumber
and dissimilar metals.
Plastic, builders'
felt, bituminous paint, caulking, or gasket material
may be used to separate panels from treated wood and
dissimilar metals. When using aluminum panels in
direct contact with steel, use one of the above
methods to separate the two metals.
Fertilizer, lime,
acids, feeds, manure, soils, and many other
substances also cause corrosion in metal panels.
Contact between metal panels and any potentially
corrosive materials should be prevented.
Porous insulation
board may absorb and retain moisture, and requires a
vapor barrier similar to that described above. This
vapor barrier should be installed such that moisture
is prevented from contacting both the insulation and
the metal panel.
FABRAL's
translucent panels are intended for siding
applications only. In
all situations, foot traffic should be avoided on
translucent panels. Translucent panels used in
roofing applications will break down over a short
period and stain metal panels below, eventually
causing corrosion of the metal. If used on roofs,
use butyl caulking to separate the fiberglass from
the metal. The fiberglass panels should be sealed
regularly, as recommended by the translucent panel
manufacturer.
Purlins,
Girts and Roof Deck
The material to
which the metal panel is fastened should be properly
spaced and sufficiently thick to provide a roof or
wall system able to meet required design loads. Load
tables are available for all FABRAL panels. FABRAL
recommends spacing the purlins a maximum of 24"
on-center for roofing (note that 5V requires solid
decking).
In re-roofing jobs
where the condition of the old decking is in
question, or where existing shingles will be left in
place, new 2x4 purlins should be fastened through
the decking and into the rafters. This will provide
a solid framework for attaching the metal panels.
A 2" nominal
lumber thickness provides the maximum pullout values
for both screws and nails when the fasteners achieve
a minimum of 1" penetration into the wood.
(Note that 1" nominal lumber is only 3/4"
thick and, therefore, results in lower pullout
values. Refer to the tables on page 30 for
additional information). Pullout values may decrease
slightly if the fasteners protrude completely
through the purlins or girts. Kiln-dried softwood is
recommended for purlins, girts, or decking (pine,
fir, hemlock, and spruce). Hardwoods are difficult
to fasten into without splitting and contain acids
that are corrosive to metal panels. Green
(non-kiln-dried) lumber may warp, twist, and shrink
as the wood seasons fully, causing waviness in the
panels and loosening of the fasteners.
Roofing
Sidelaps should face
away from wind driven rain. Therefore, begin
installation by installing the first sheet square
with the eave and gable at the downwind end of the
roof, farthest away from the direction of prevailing
winds.
In applications
requiring a panel endlap, please refer to the
details shown on page 12 of this manual. For best
results, lap panels as shown and install in the
indicated sequence. All
endlaps require sealant. When
weathertightness is critical, use sealant tape in
all sidelaps. See FABRAL's F-102 Installation Guide
for more information.
To provide a drip
edge, allow an overhang of 1" to 2" at the
eave. At the gable edge, use a
gable or sidewall flashing. This will keep
weather out, prevent lifting in high winds, and
provide a neat, finished appearance. The trim and
roofing sheet should be fastened every 6" to
10" inches along the gable edge.
Roof
Pitch
The metal roofing
panels shown in this manual require a minimum pitch
of 2-1/2" per foot to ensure proper drainage.
Refer to the F-102 Installation Guide for the
suggested endlap and the suggested "horizontal
projected roof lengths" that apply to the
various panels. For wider buildings and lower roof
pitches, contact your FABRAL dealer for other
suitable FABRAL profiles.
Bending
and Bowing
Aluminum roofing and
siding sheets are rollformed from hardened, tempered
metal for maximum strength. If a sheet must be bent,
a gentle 90-degree bend is the maximum recommended.
Metal should not be re-bent once it has been formed,
nor should it be folded back on itself, since it is
not designed to take a lockseam. When a metal
roofing sheet must be installed on a curved roof,
screws should be installed at every overlapping rib
at the sheet ends to resist the natural tendency of
the metal to spring back. Standard fastener spacing
is permitted over the rest of the sheet. When
installing the metal roofing and siding panels shown
in this booklet over a curved arch, the minimum
radius of the arch is 18' for aluminum profiles and
24' for steel profiles. Use sealant tape or butyl
caulking at all sidelaps and endlaps.
Additional care and
fasteners must be provided when securing the top and
bottom purlins on a laminated rafter building to
prevent the curved panels from pulling the purlins
loose from the rafters. Ring-shank pole barn nails,
heavy wood screws, lag screws, or bolts are often
used for attaching these purlins.
Siding
Siding should be
installed using the standard fastening and overlap
patterns to ensure optimum performance. For strong,
neat corners use hemmed corner flashings.
Do not run siding
sheets all the way to the ground.
Instead, provide a protective base of
concrete, masonry, treated wood, or similar material
12" to 18" from ground level and end the
siding sheets there.
If siding sheets are
installed horizontally, use sealant tape or butyl
caulking at the vertical laps to ensure weathertight
joints. Install panels from the bottom up so that
water is directed away from, and not into, the lap
joints.
Fastening
FABRAL can supply
either screws or nails for fastening into dimension
lumber, with screws offering better pullout values.
Woodgrip screws for use with steel panels are
galvanized and then coated with an organic polymer
for optimum corrosion resistance. For best results
with aluminum panels, use #300 series stainless
steel Woodgrip screws.
The FabrOseal®
galvanized ring-shank nail, with its premium
long-life silicone rubber gasket, assures a lasting
seal and is the best nail available for steel panels
when screws are not desired.
The correct way to
fasten steel panels with nails is to drive the nail
through the top of the rib so the washer is
compressed securely against the metal. Nail
placement must be in the ribs for roofing
applications to minimize the potential for roof
leaks. Over-driving the nail can split the washer
and dimple the metal, causing leaks.
Wood screws with
combination metal and neoprene washers should be
installed in the flat area of the panel adjacent to
the ribs, and tightened such that the washer is
compressed as illustrated above. This will ensure a
lasting, leak-proof seal. See pages 4 to 5 for the
correct fastener locations.
Safety
Always work safely
when installing metal products. Use extreme caution
on the roof at all times, and wear gloves and safety
glasses to avoid injury. Hearing protection should
be used when power-cutting metal panels. Do not walk
on panels until all the fasteners are installed.
Metal panels are slippery when wet, dusty, frosty,
or oily. Do not attempt to walk on a metal roof
under these conditions. Wear softsoled shoes to
improve traction and to minimize damage to the paint
finish. Always be aware of your position on the roof
relative to any roof openings, roof edges,
co-workers, and penetrations. Installing metal
panels on a windy day can be dangerous and should be
avoided. Consult OSHA guidelines for more complete
safety requirements.
Cutting
Aluminum Panels
To make a cut
parallel to the ribs, score the panel deeply with a
sharp utility knife and bend back-and-forth along
the score, breaking the metal off cleanly. For cuts
across the ribs, use straight-cut snips, electric or
pneumatic shears, a portable profile shear, or an
electric nibbler. Some installers prefer using a
circular saw with a metal cutting blade (a finetooth
hardwood blade, or a standard combination blade
reversed in the saw works also). Light oil or soap
on the blade will make cutting easier.
Cutting
Steel Panels
Steel panels may be
cut with straight-cut snips, electric or pneumatic
shears, a portable profile shear, or an electric
nibbler. Some installers prefer using a circular saw
with a metal cutting abrasive blade. This method may
be faster, but it has some drawbacks: 1. Saw cut
edges are jagged and unsightly and tend to rust more
quickly than sheared edges 2. Saw cutting produces
hot metal filings that can embed in the paint and
cause rust marks on the face of the panel 3. Panels
to be saw cut must be turned face down and cut in a
location down-wind and well away from the building
and other panels to avoid embedment of metal filings
on other panels 4. Saw cut panels must be thoroughly
wiped to ensure the removal of all metal filings 5.
Saw cutting burns the paint and galvanizing at the
cut edge, leading to the onset of edge rust.
Building
Maintenance
A metal roof should
be inspected annually and cleaned as necessary to
maintain its beauty and performance. Any debris or
residue, including leaves, twigs, and dust should be
cleaned off promptly to prevent moisture entrapment
against the metal, which may lead to finish
deterioration or premature corrosion.
|